How LiDAR can be used for Industrial Range Finding
LiDAR stands for ‘light detection and ranging’ and is a technique for measuring the distance of objects away from a sensing device. The principles used are very similar to RADAR but, with LiDAR, the radio waves are replaced by light – usually laser light. The LiDAR system emits a beam of light that hits a target before being reflected back to a sensor that is located close to the light source. By measuring the time taken for the light to travel, and knowing the constant speed of light, the distance of the target can be calculated with a high degree of accuracy. This is referred to as Time of Flight (ToF).
LiDAR has been very successful within the automotive industry, particularly in the advanced driver assistance systems (ADAS) where it can be used for obstacle detection and collision avoidance, as well as adaptive cruise control (ACC) and navigation. However, a new and exciting area for LiDAR technology is for industrial range finding within the Internet of Things (IoT).
our leading LiDAR experts, Edel Cashman, applications engineer, SensL division, intelligent sensor group, shares her expertise on range finding and Silicon Photomultiplier (SiPM) technology, introducing our new SiPM dToF LiDAR Platform.
What is a rangefinder and how is it part of the Internet of Things?
A rangefinder is a depth measurement system and can be used in a wide variety of applications involving depth perception, object detection and avoidance, and location mapping.
What benefits does LiDAR technology bring to range finding?
LiDAR is highly configurable, can be used in a wide array of environments and lighting scenarios, and can precisely detect any type of solid object.
What is the Direct Time of Flight (dToF) Principle?
All LiDAR systems use light and the 'time of flight' concept to measure distance. Indirect techniques use the phase or frequency difference between a continuous and modulated light, and the reflected light. In dToF systems, a pulsed laser provides the photons that are reflected off a surface and detected by the sensor. The time difference between the laser emitting a photon pulse and the receiver detecting it gives the distance. This is typically achieved using either a time-to-analog or time-to-digital converter. By implementing time-to-digital conversion using an FPGA, you can accurately register the time at which emission begins and measure when the first detected return photon is received after reflection from the target object. For long-range detection, highly sensitive photodetectors are essential.
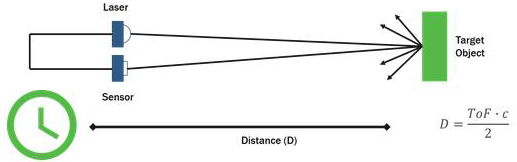
Why is Direct Time of Flight (dToF) better suited than Indirect Time of Flight (iToF) for IoT applications?
Both iToF and dToF have advantages in range finding. dToF is simple to implement in terms of illumination, detection and processing, and it requires a short computation time. A dToF system is capable of distinguishing multiple objects within a Field of View (FoV), and does not suffer from range ambiguity due to phase cycle.
What benefits does SiPMs offer compared to other technologies?
SiPMs are highly sensitive photodetectors with low noise and fast response time. SiPMs provide highly accurate ToF and intensity information from a single measurement. ON Semiconductor SiPMs are highly uniform and low cost, making them suitable for high volume production. The design of an SiPM based system is simple, reliable and scalable. High Near Infrared (NIR) sensitivity means ON Semiconductor SiPMs can be designed into systems with low-cost mass production laser diodes within the 850 nm to 940 nm wavelength range.
What are some challenges associated with the development of a range finder application?
There are many challenges associated with developing range finding applications. For low power applications, the photon budget may be limited. For long-range systems the laser source can be optimized by using a shorter laser pulse width for the same average energy, - short pulse widths are easily detected by the SiPM. Multi-point range finding will necessitate scaling up of the number of detectors or adding a scanning (beam steering) mechanism to a single point detector – SiPM high bandwidth and fast response time enable high frame rates in scanning scenarios.
Minimum range detection can also be a challenge in range finder design. Other challenges are optics cost, and laser uniformity over a wide temperature range.
SiPM dToF LiDAR Platform
What is Industrial Rangefinding?
The SiPM dToF LiDAR Platform is a single point range finder development kit that is cost-optimized for mass deployment in industrial and consumer applications. It provides a simple way to implement direct depth sensing and distance measurement in IoT applications. The kit is based on the latest RB-Series Silicon Photomultiplier (SiPM) detector, which is a near-infrared (NIR) single-photon sensitive, high-performance solid-state sensor.
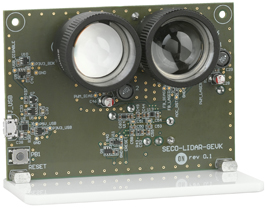
The RB Series SiPM sensor developed by ON Semiconductor and used in our platform has high (1x106) gain and high photon detection efficiency (10% at 905 nm) in a compact, rugged and magnetically insensitive package. It achieves its high gain with a very low bias voltage of around 30V, with a noise level almost entirely in the single-photon range. The high level of uniformity between microcells achieved by ON Semiconductor means the sensor is able to discriminate the precise number of photons detected as distinct, discrete levels at the output node.
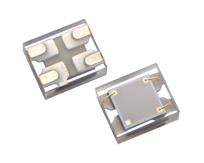
RB-Series SiPM
The target distance of the reference kit is between 11 cm and 23 meters. It features plano-convex lenses optimized for 650 to 1050nm signals with a 905 +/- 5nm bandpass optical filter and 905nm laser diode transmitter.
The reference kit works out of the box, using a PC-based GUI (provided). It also features an industry-standard PMOD connector for creating a complete solution, which can also provide the power supply needed. Alternatively, the reference kit can be powered by a USB connector. The GUI allows many of the settings to be modified, allowing the platform to be used in a wide range of industrial and IoT applications.
Learn more about the SiPM dToF LiDAR platform, or check out these design resources below.
Design Resources:
- SiPM dToF LiDAR Platform Getting Started Guide
- RB-Series SiPM Datasheet
- Introduction to the Silicon Photomuliplier (SiPM) Application Note
- SiPMs in Direct ToF Ranging Applications White Paper